Use of low impact development (LID) is growing in both new developments and retrofit projects. This increase also means a growing need for contractor experience related to unique stormwater management requirements of LID. While construction is critical to long-term LID performance, success ultimately depends on designers, installers, developers, and inspectors understanding LID and coordinating across all phases of a project.
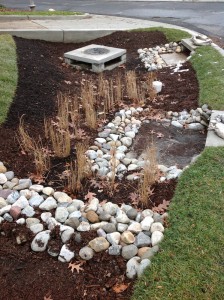
The fall installation of a bioretention facility in Montgomery County. Sediment collects on the concrete cleanout pad for easier maintenance with a flat-headed shovel. Image credit: Montgomery County, Md., Department of Environmental Protection
Before construction
Successful LID construction begins with designers, contractors, and project owners being on the same page. “At the start of the project, we have a preconstruction meeting for owners and designers to review issues related to managing water onsite,” said Rick Scaffidi, vice president at Environmental Quality Resources LLC (EQR). “It is important to ensure that all practices are constructed in a way that promotes both sidewall and bottom infiltration from the site. We have to ensure that the rate is consistent, and that the practice works.”
Scaffidi also advocates for proactive design plans with designers visiting and surveying the construction site. However, “owners may not always pay for field work to confirm plan sets will perform as designed,” Scaffidi said.
While EQR specializes in environmental construction with crews trained in multiple disciplines — from pipework to soils to landscapes — this is not always the case for construction crews.
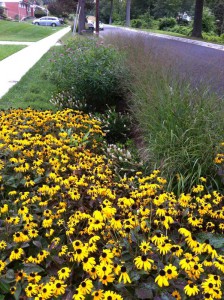
Dense plant cover stabilizes this retrofit and adds other environmental benefits to the streetscape. Image credit: Montgomery County, Md., Department of Environmental Protection
“It is important for the contractor to understand the design intent of LID practices, along with the water quality and water quantity goals and objectives of the project,” said Chris Rust, project manager and engineer with Strand Associates Inc. “For example, conveying the importance of a bioretention soil media and how it provides water quality treatment helps contractors understand why it is important to keep the system clean, uncompacted, and performing as intended.”
Designers can minimize delays by providing oversight and guidance during construction. “Often there is a significant emphasis on the design phase of the project, but it is also important to understand the value of construction observation following the design,” Rust said. “The construction phase is one of the key components of a green infrastructure project, and thorough construction observation is critical to the overall success of the project.”
In some cases, designers also can provide inspection services to ensure contractors follow construction specifications, if the owner is willing to pay for it. The construction guidelines from the Interlocking Concrete Pavement Institute (ICPI) include an inspection checklist for building permeable interlocking concrete pavements, said David R. Smith, ICPI technical director.
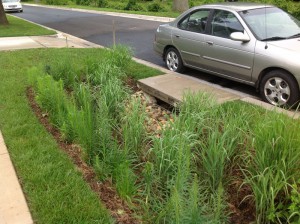
Switch grass is planted around the inlet to act as a strainer for entering silt and trash, enabling easier maintenance of the inlet. Image credit: Montgomery County, MD, Department of Environmental Protection
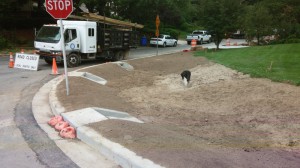
In this bioretention retrofit, storm drain inlets are protected prior to planting. Image credit: Montgomery County, Md., Department of Environmental Protection
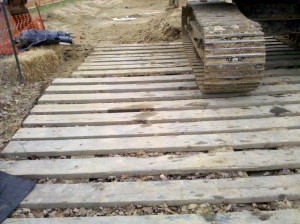
Ground protection during bioretention retrofit construction. Image credit: Montgomery County, MD, Department of Environmental Protection
Montgomery County, Md., has overseen various types of LID projects, from small homeowner installs to large retrofits funded by capital improvement budgets. For larger projects, it is very important for the construction foreman to stake out the site, said Ann English, Montgomery County RainScapes program manager. Further, it is important for “the designer and construction manager to communicate well,” she said.
English also described the important link between design, construction, and maintenance. “Traditionally, these have been very different phases, but with LID, planning for maintenance is really important to long-term success,” she said. For instance, placing permeable pavement under tree canopies could cause clogging without additional surface cleaning in autumn when leaves fall. Since LID practices are dynamic systems, the sooner routine maintenance procedures are established, the better.
Common construction challenges
In constructing LID as part of a larger development, contractors must troubleshoot to avoid delays. An example is working around utilities, especially when constructing LID in the public right-of-way. These areas must be hand-dug or vacuum-excavated to avoid utility line damage. To accommodate utilities, contractors often must adjust the practice footprint or depth.
Most LIDs are built at the end of a construction project, so disposal of soil and debris that cannot be used elsewhere affects costs. “The disposal of soils can be quite expensive,” Scaffidi said.
For bioretention facilities, another common need is grading the site so that it drains properly into the facility. Particularly in private development — where there is more flexibility in managing earthworks than in commercial or transportation projects — regrading may change elevations from the original design. This can result in a different drainage area flowing to the facility or may increase the earthworks required to meet design goals. “If you don’t have a current survey, you need to make sure that you resurvey and double-check elevations,” Scaffidi said.
Further, LID underdrains that discharge into an existing storm drain distribution box or catch basin can raise concerns. “One of the most significant problems we come across is that the actual drainage systems do not always match up with the design drainage structures,” Scaffidi said. “In those cases, we have to reconcile the differences and come up with a correction strategy.” To reduce problems in the field, it is important to check the invert elevations of connecting pipework before beginning a project. Scaffidi said he recommends a site survey during the design phase, “that way you have accurate information going into construction.”
Further, selecting proper equipment is essential. For instance, toothed buckets are needed for excavation to fracture the soil rather than shear it. This prevents compaction and sealing of side or bottom soils, particularly in high clay soils. In vegetated systems, equipment cannot be placed on the footprint of the facility, so site access is limited to the practice’s edges. This is not the case, however, for permeable pavers.
According to Smith, one of the most common installation issues for permeable interlocking concrete pavement (PICP) is settlement due to inadequate compaction of the open-graded aggregate subbase, base, and concrete pavers. This can happen when large vibratory rollers are not used or when small vibrator plate compactors are used instead of large ones.
Keeping the completed PICP surface clean and free of sediment during construction also is important. “This can be done by covering the finished surface with geotextile and washed aggregate, and then removing it when adjacent construction is completed,” Smith said. “Other approaches include building temporary roads for construction traffic or using the PICP for construction traffic and then cleaning the surface with a vacuum machine when construction is completed.” Visit www.icpi.org for more guidance.
Rain also can pose difficulties during construction, as ponding of sediment can seal the soil subgrade under a practice. “If we have rain after excavation, we re-till the bottom of the practice, or if puddling of mud occurs, we excavate or remove the mud and backfill with porous material,” Scaffidi said.
In some cases, LID facilities are used initially as a sediment trap and later converted to a practice — often, a bioretention facility. Due to erosion and sediment buildup, however, contractors have to excavate wet sediment, so the practice can drain to parent soils. Some jurisdictions do not allow pre-digging because “regulators are concerned that the material will not be cleaned out properly,” Scaffidi said.
Protecting LID retrofits
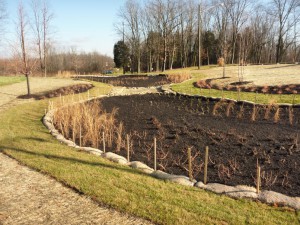
Erosion prevention and sediment control measures around bioretention basins at the University of Cincinnati’s Clermont College campus. Image credit: Chris Rust, Strand Associates, Inc.
When a practice is built new or as a retrofit, LID facilities must be kept clean and the infrastructure around the facility protected. Erosion and sediment controls such as silt fences, straw wattles, erosion control blankets, and perimeter sod can help keep practices from getting clogged.
“One of the most common challenges during and after construction of LID facilities is keeping sediment out of the system during rainfall events,” Rust said. “When erosion protection and sediment control measures are not maintained throughout the duration of construction, it only takes one big storm event to convey sediment from the tributary area onto the surface of the green feature. Once that happens, the practice can clog and won’t promote infiltration as desired.”
In addition to erosion protection and sediment control, construction sequencing also is an important consideration. “Ideally the area upstream from the LID facility should be fully stabilized and vegetated before the placement of key components, such as the bioretention soil media,” Rust said. “If the schedule permits, allow vegetation to germinate first.”
Though the practice is functioning successfully as intended now, one of Rust’s more challenging projects from a sequencing aspect was the design and construction of 12 terraced berms in Northern Kentucky.
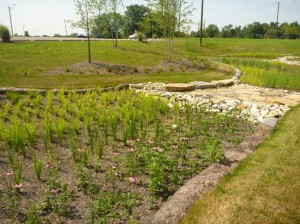
Establishment of vegetation around and within bioretention basins at the University of Cincinnati’s Clermont College campus. Image credit: Chris Rust, Strand Associates, Inc.
“Keeping sediment out of the bioretention soil media was difficult due to site challenges, such as steep topography, as well as the unique challenge of constructing the berms in series,” Rust said. “Some vegetation initially did not survive because of sediment buildup in the system, which required the need for replacement.” Despite construction challenges, the project was recently recognized with a national honor award for innovative stormwater management.
If erosion and sedimentation does occur, the layer of sediment can be removed without completely replacing the soil media. However, “if plants have already been installed, it’s challenging to remove sediment around and in between existing plants,” Rust said. “This ties back into scheduling. It can be beneficial to wait for plant installation within the LID facility until the surrounding areas are stabilized and vegetated.”
According to Rust, sedimentation affects vegetated systems more often than pavement retrofits, particularly when the newly installed pavers are surrounded by impervious surfaces and runoff onto them is not carrying much sediment. However, permeable pavement can be prone to clogging in urban settings with existing tree canopies and other vegetation upstream.
Training
In some areas, the demand for experienced LID installers is growing faster than the supply. Communities and companies are struggling find qualified contractors. Private and quasi-private developments usually do not require certified contractors. Yet mistakes made during the construction phase and growing construction demand, demonstrate a need for training and certified contractors as well as good communication and coordination throughout all stages of the project.
Communities and associations, however, are stepping up to provide training and create a pool of qualified contractors. For example, Montgomery County offers specialized RainScapes training for landscape professionals and other LID installers. The county also has partnered with Montgomery College to develop fundamental skills for building and installing bioretention systems, stream restoration projects, permeable pavements, and other LID practices.
ICPI’s one-day contractor course on installing PICP is another example. “We’ve had over 1000 contractors take this course,” Smith said. In combination with a basic installation course, an exam, and experience requirements, contractors can receive a Certified Installer PICP specialist designation from ICPI. The institute also provides free PICP construction guidelines, detail drawings, and specifications online as well as paid software tools and manuals for designers.
Do you have other good examples of LID construction resources and training opportunities? Let us know about them in the comments section below.